Newsletter Signup - Under Article / In Page
"*" indicates required fields
The biologics industry is growing at an incredible rate. While its global market value was estimated at $236B in 2017, it is expected to rise to $310B by 2023. As key market players enter the field, competition is increasing.
In recent years, the biologics industry has become more versatile and has moved from being primarily antibody-focused to including other modalities, such as bispecific antibodies, fusion proteins, gene and cell therapies, and exosomes. The momentum is picking up, and successful biological therapies are hitting the market more frequently.
Facing challenges in biologics development
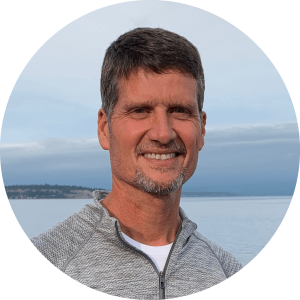
However, despite their success, biologics come with a number of challenges. The cost of biologics development has greatly increased. This means that researchers face the challenge of developing successful drugs while reducing costs, keeping biologics affordable, and potentially improving access to patients at the same time. “Price increases are unsustainable,” says Dean Pettit, Senior Vice President of Biotherapeutic Sciences at Just – Evotec Biologics. “In order to improve global access to biotherapeutics, we need to apply technologies that can reduce the current development cost structure and create competition that lowers prices.”
In addition to lowering costs, there is also a struggle to reduce the cycle times for drug development, which are extremely lengthy, with some drugs taking over a decade to be developed. “Cycle times in drug development are too long,” Pettit explains. “We need to think about ways of reducing cycle times with the application of new technologies, such as high throughput robotics and machine learning algorithms to reduce time-consuming development activities.”
With the growing complexity of biologics and their development, larger companies are also facing data management issues. Here, the existence of silos can cause physical and decision-making separations within organizations, resulting in prolonged development timelines and higher costs.
“While there are many advantages to developing drugs in a large company, it can also be challenging because of the existing silos,” Pettit explains. “Hand-offs occur between different departments and teams can become isolated from one another. Even the data systems each department uses to collect information and to communicate with each other can differ. The silos in large organizations can make data sharing between groups challenging, if not impossible. There needs to be a greater focus on making data available to everyone from a single integrated platform.”
Addressing the challenges of biologics development with a centralized data management system
Aware of these lingering challenges within the biologics industry, Just – Evotec Biologics is using cutting-edge technologies to lower drug development costs and shorten cycle timelines to improve patient access. Moreover, Just – Evotec Biologics prides itself on full integration of all aspects of its business, including its technology platform, data sharing, collaborative lab and office spaces, and its fully integrated technology platform called J.DESIGN.
“At its core, J.DESIGN is a common data management system that centralizes and integrates the highly complex datasets generated from the distinct activities involved with the development and manufacture of biologics,” says Pettit. “In essence, J.DESIGN accelerates the development of high-quality biologics and provides manufacturing process control at the lowest possible cost.”
This integrated technology platform comprises all the important activities required for biologics development
J. DESIGN integrates molecule discovery, molecular optimization, process and product development, and manufacturing. Leveraging the J.DESIGN platform, potential partners are offered specific or end-to-end services.
“The experts operating J.DESIGN have worked within the industry for decades. J.DiscoveryTM contains large, diverse, manufacturable, and developable discovery libraries, and uses machine learning to generate antibodies which are manufacturable,” Pettit says. “Our molecule design team, J.MDTM, optimizes parental antibody sequences to enhance manufacturability and stability to save time during process development. J.MDTM uses an in-house suite of computational tools called Abacus that can assist in designing the best molecules and predict the best conditions for development.”
Prior to molecule optimization, Just – Evotec Biologics also offers its customers an in silico risk assessment for developability and manufacturability. Using the Abacus toolset, the team can look at a molecule’s sequence and predict possible liabilities or issues that might occur during downstream process development. This allows the team to react and solve issues early.
Optimized processes save time and costs
J.DESIGN also focuses on process and product design. “JP3® stands for Just process and product platform,” Pettit says. “The process development scientists working on JP3® are experts in cell line development, upstream bioreactor, downstream purification development, analytical method development, drug product and formulation development, as well as processing formats, such as intensified fed-batch and continuous processing.”
The JP3® scientists utilize high throughput robotic solutions for process and product development and leverage data for learning and prediction,” Pettit explains. “Analytical capabilities include high-resolution mass spectroscopy tools. Process and long term storage, which are traditionally determined through formulation activities, are defined in J.DESIGN during molecule optimization activities, J.MDTM.”
Just – Evotec Biologics has developed a small, flexible, low-cost facility solution to biotherapeutics manufacturing called J.POD. “These small-footprint facilities tie together all of the elements of J.DESIGN,” says Pettit. The company has a cGMP clinical manufacturing facility that is co-located with its lab and office space in Seattle, Washington. Just – Evotec Biologics is also currently planning a commercial J.POD manufacturing facility in Redmond, Washington which will increase its capacity.
The future of the biologics landscape
Just – Evotec Biologics is currently working on some exciting projects. “Many biotherapeutics require large scale production at low cost to enable their commercialization,” says Pettit. “This holds true for many infectious disease therapeutics, such as our work to develop broadly neutralizing antibodies for the prophylaxis of HIV, where low costs are critical for their success. We are also working on antibodies for oncology and auto-immune disorders.”
The life sciences industry is moving from huge blockbuster drugs to smaller market sizes, personalized medicines, and combination therapies. This also means that the quantities of manufactured drugs are decreasing and the manufacturing process does not occur in large facilities but can be executed in smaller facilities, such as the ones that Just – Evotec Biologics has built.
“Where we’re headed as an industry is smaller-scale manufacturing that is more versatile and has more flexible manufacturing requirements,” says Pettit.
Are you interested in learning more about biologics development and manufacturing? Check out Just – Evotec Biologics’ website or get in touch with their expert team!
Images via Shutterstock.com and Just – Evotec Biologics