Newsletter Signup - Under Article / In Page
"*" indicates required fields
Swiss researchers are developing cellulose-based materials for 3D bioprinting, which could lead to implants such as prosthetic ears.
3D-printed implants have big potential in the field of regenerative medicine. Although still at an early stage, this technology is enabling the development of customized prosthetics, such as skin and joint cartilage. One big focus in the development of 3D bioprinting is how to make the printable material non-toxic and conducive to the regrowth of tissue.
A research group from the Swiss Federal Laboratories for Materials Science and Technology (Empa) is investigating wood-derived cellulose as a potential implant material due to its strength, abundance in nature, and lack of toxicity for human tissue. They are combining the cellulose with hydrogels to make a 3D-printable material that can be used to make customized implants.
“Hydrogels are great mediums for cell proliferation and growth. However, as they mostly consist of water, they lack the required mechanical properties.” Michael Hausmann, one of the researchers involved in the work, told me. “We reinforce hydrogels with cellulose to improve the mechanical properties.”
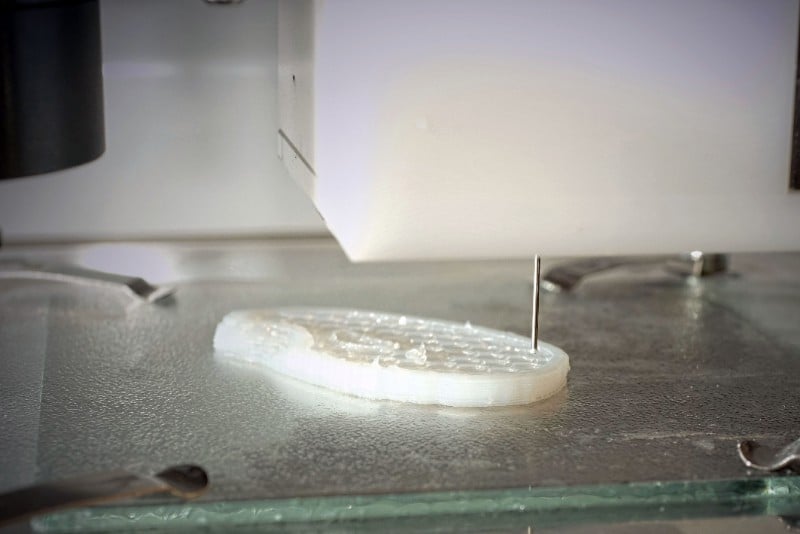
This cellulose-hydrogel material could have many applications in tissue engineering, but the easiest to start with for the group is a prosthetic ear. “Cartilage from the ear is the simplest candidate as the mechanical constraints are not as challenging as compared to knee joints, for example,” Hausmann said. Once the group has optimized this application, the group can turn its attention to others, such as cartilage implants in knee joints for patients with arthritis.
The researchers make up one of several groups worldwide investigating the potential of cellulose as an implant material. Hausmann argues that their method has an advantage over those of other groups. “We can play with the quantity of cellulose where we want and how we want, to specifically define the mechanical properties.”
The group has lots of work to do before it can begin commercializing this technology, but it is open to collaborations with corporate partners to advance the development.
There is lots of corporate interest in 3D bioprinting. Last year the French tissue engineering company Poietis began collaborating with the Katholieke Universiteit Leuven, Belgium, to develop implants helping with skeletal regeneration. The Russian company 3D Bioprinting Solutions is working on making the 3D bioprinting process faster by levitating cells with magnets, and is part of a collaboration that recently bioprinted a mouse thyroid gland in outer space.
3D bioprinting of organ implants is currently at an early stage across the board, and getting an implant to work inside the dynamic environment of the human body is a very complex task. Hausmann remains confident that research will be able to tackle the challenge. “This field is definitely going to see amazing developments over the coming years,” he concluded.
Images from Empa